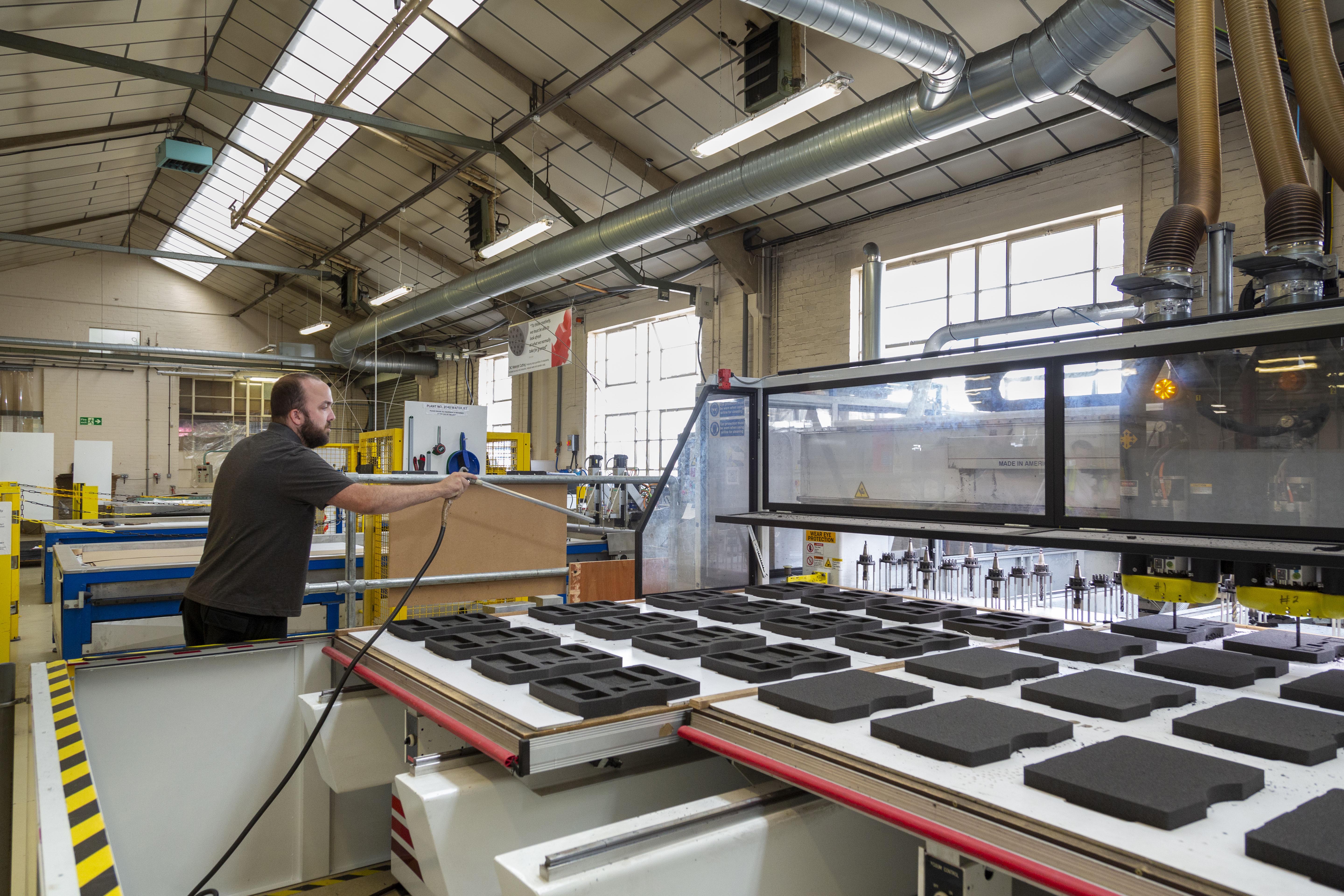
Quality at Kewell Converters
Kewell Converters is committed to delivering high-quality foam solutions to a vast variety of sectors. Central to our success is our focus on quality, which we believe is crucial not just in producing outstanding foam products but in fostering long-term relationships with our clients.
By prioritising excellence in every aspect of production, we ensure that our customers receive unparalleled service and products that set the standard in the field.
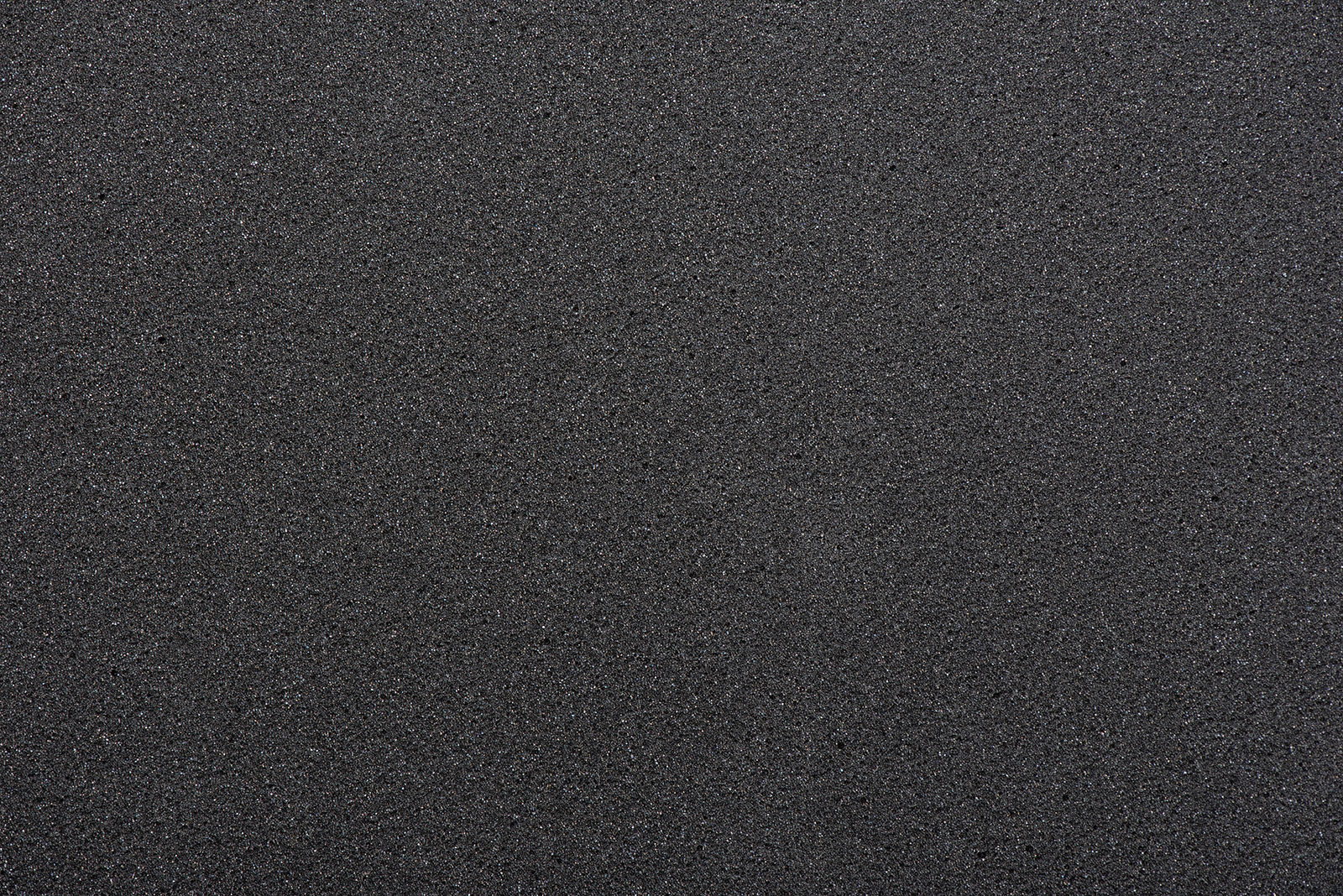
"Quality is one of the cornerstones of the Kewell ideology. It’s why many of our customers come back time and time again. We use various measures to ensure that parts we make are of the highest quality. Whether it’s taking and documenting part dimensions at every step of the manufacturing process or ensuring that all our machinery is in the very best condition. Quality is our compass, guiding us in every decision and action we take."
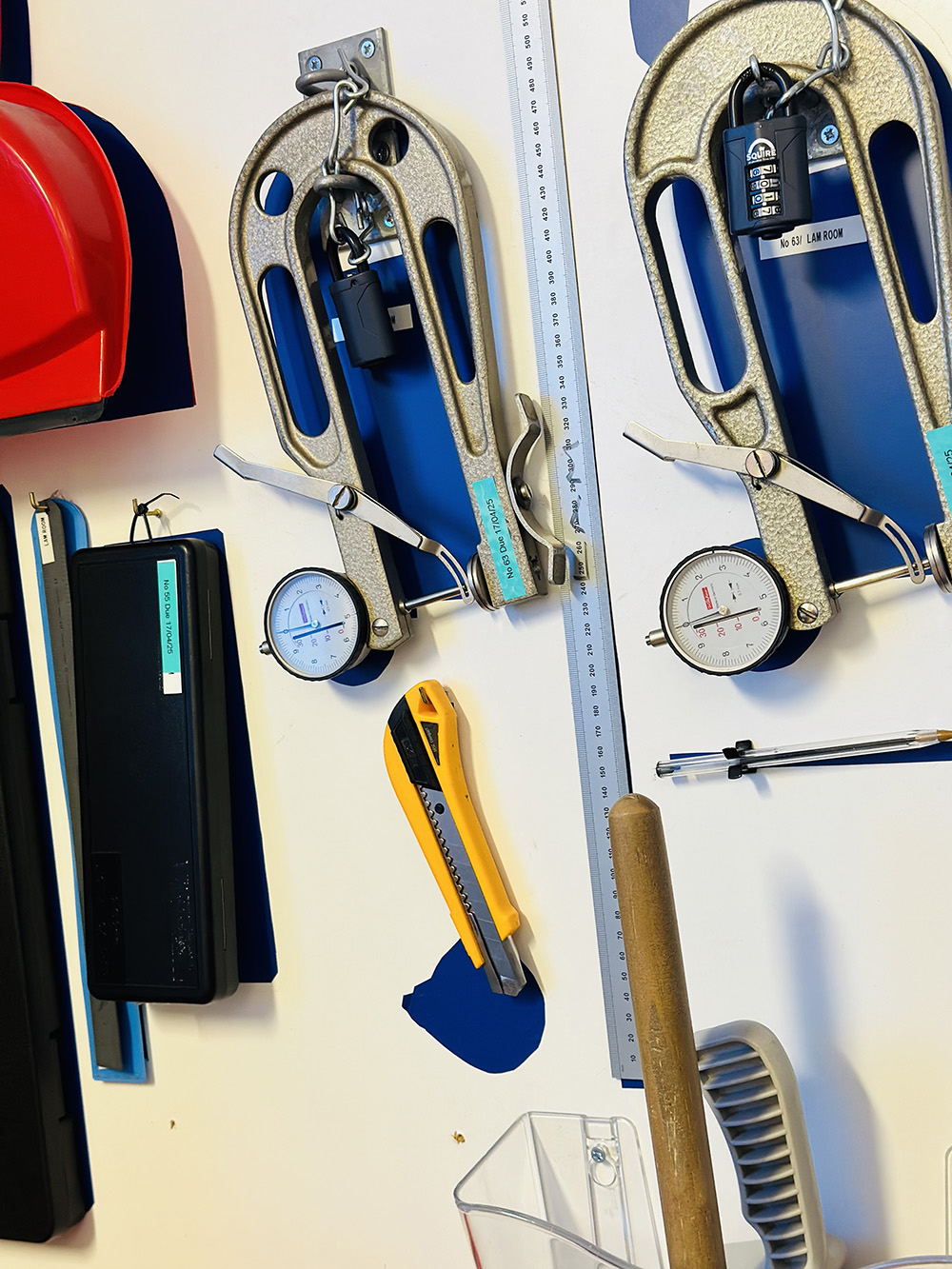
Backed by ISO accreditations
Furthering customers’ peace of mind are certifications from ISO 9001: 2015 Quality Management System which we’ve had and maintained for over 20 years and ISO 14001:2015 Environmental Management System which we added to our bow in 2019, to ensure quality assurance standards at every stage of production. We also publish an Environmental Statement which you can view here. We’re exceptionally proud of maintaining these over the years and the vigorous audits performed.
We have a Quality Management System that continuously improves our effectiveness in maintaining our BS EN ISO 9001-defined requirements. We comply with all relevant standards and regulations and are committed to delivering high-quality products and timely deliveries to ensure customer satisfaction.
Our biggest achievements are maintaining ISO accreditations and introducing Standard Operating Procedures which improve and control our manufacturing processes.
I can’t thank you enough for your care and attention to detail. I know you have all gone the extra mile for us, and I am extremely grateful. The quality of the parts has given our business the best possible start and will make a huge impact on the lives of the children who will be using our seating soon.
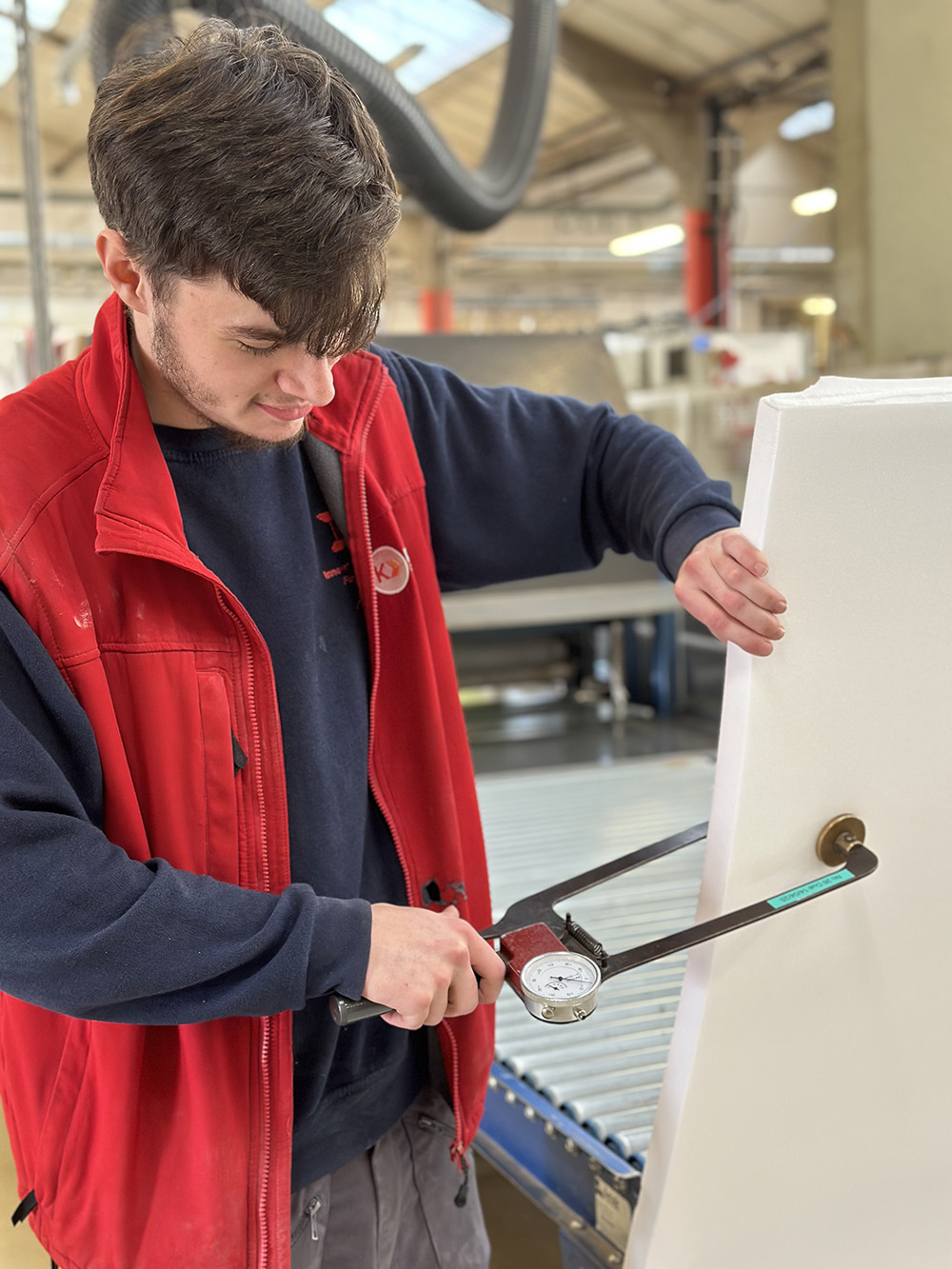
Our quality assurance commitment
At the helm of our quality initiatives is our dedicated Quality Manager. This role is pivotal in embedding quality in every stage of the production process, ensuring that every product meets our stringent requirements in the vast array of sectors we work with that require the upmost precision from the defence and aerospace industry through to the healthcare and industrial sector.
Our commitment to quality assurance means that from the initial design phase through to final production, robust quality control measures are in place. This meticulous approach guarantees that we consistently deliver the highest quality products, reflecting our pledge to excellence.
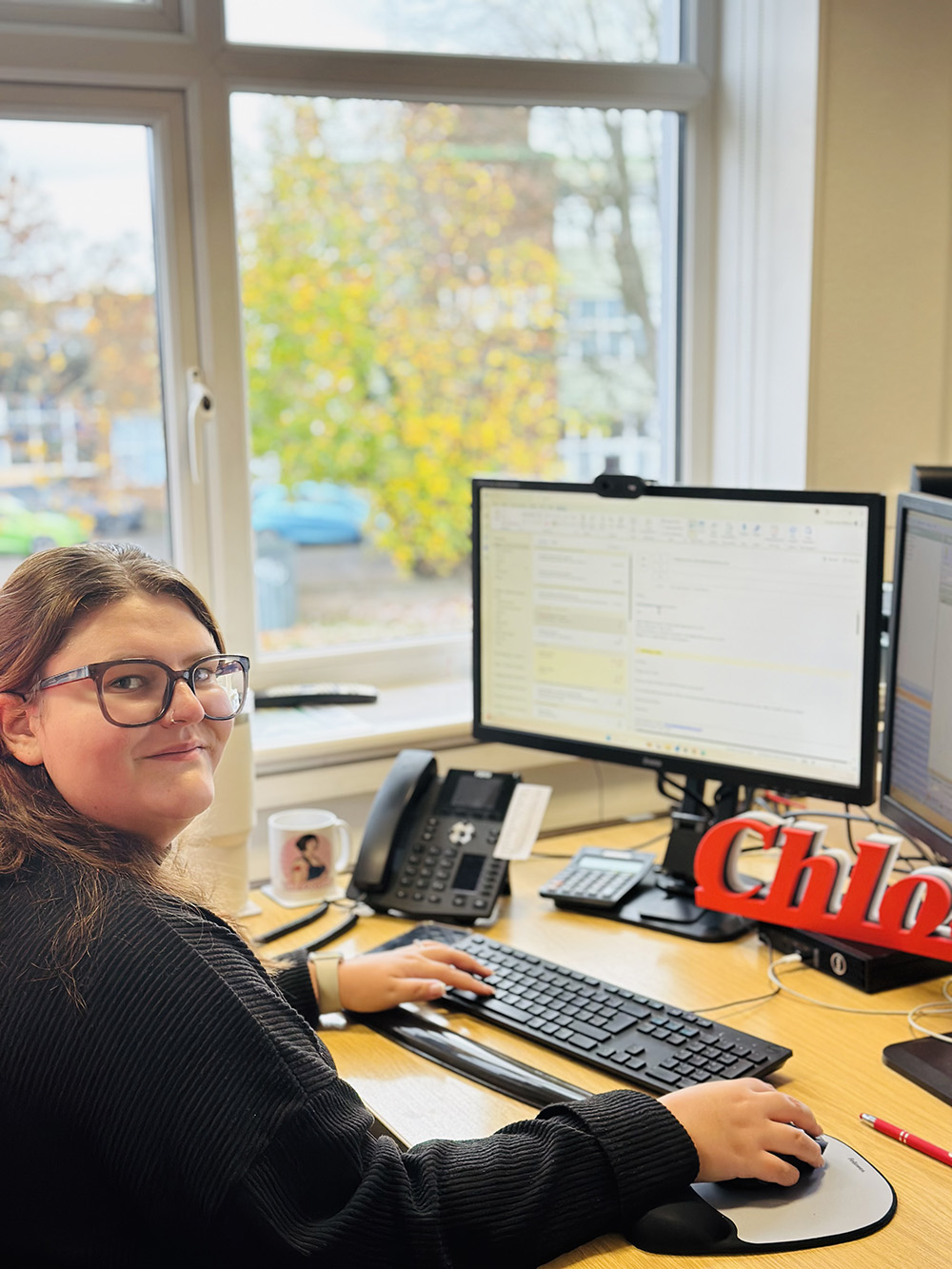
Our customer charter
Our customer charter serves as a cornerstone of our customer service philosophy, outlining the fundamental values of reliability, trustworthiness, and quality that underpin every customer interaction. This shows the high standards you can expect from Kewell Converters.
At Kewell Converters, quality isn't just a promise—it's a tradition. For over five decades, we've honed our precision and attention to detail, backed by an experienced team and robust processes. As a family-owned business, we pride ourselves on offering a personal, agile service, responding swiftly and effectively to the needs of our clients. This dedication to quality is what makes us a trusted partner in the supply chain, delivering complex foam solutions that not only meet but exceed expectations.
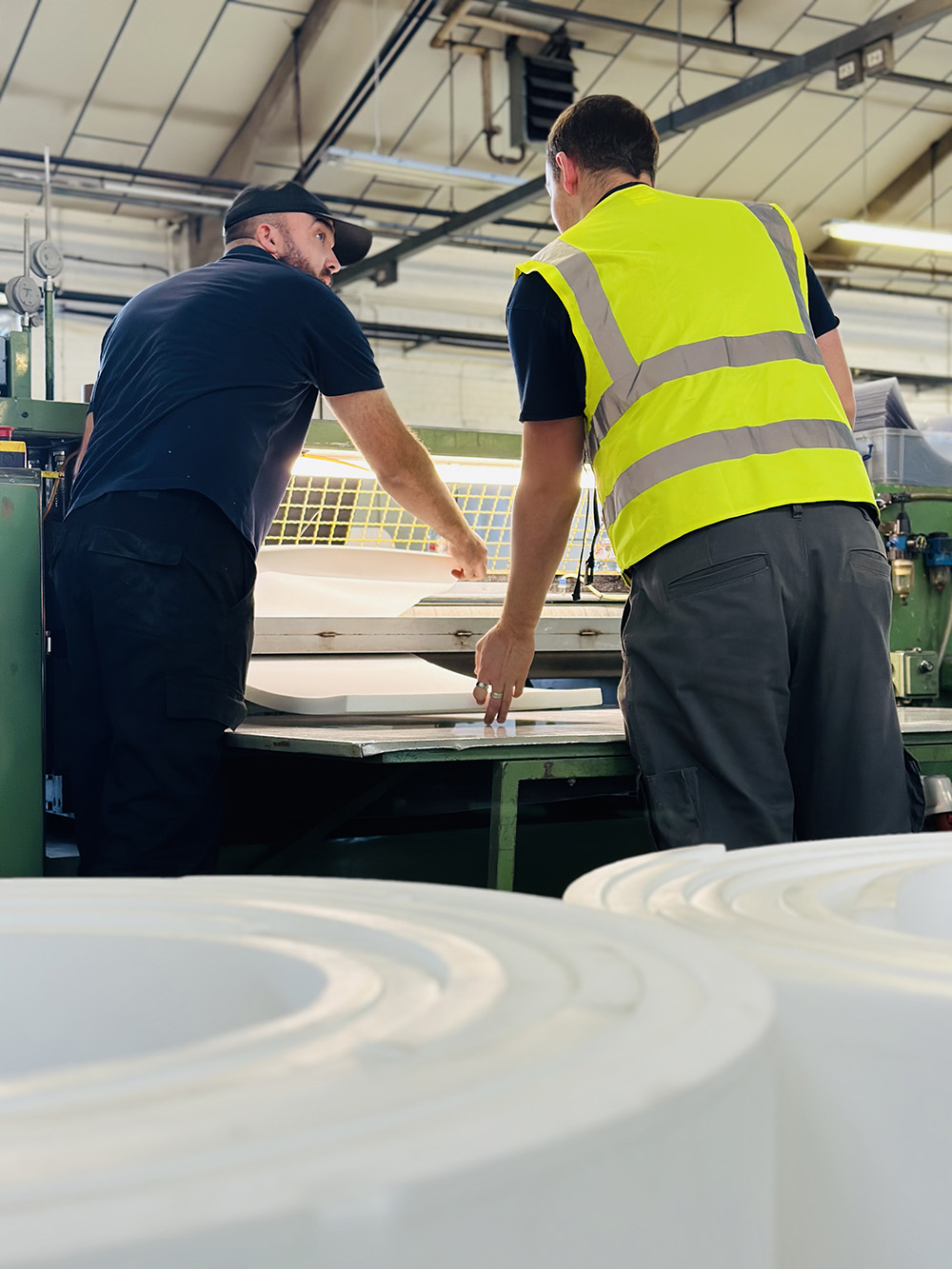
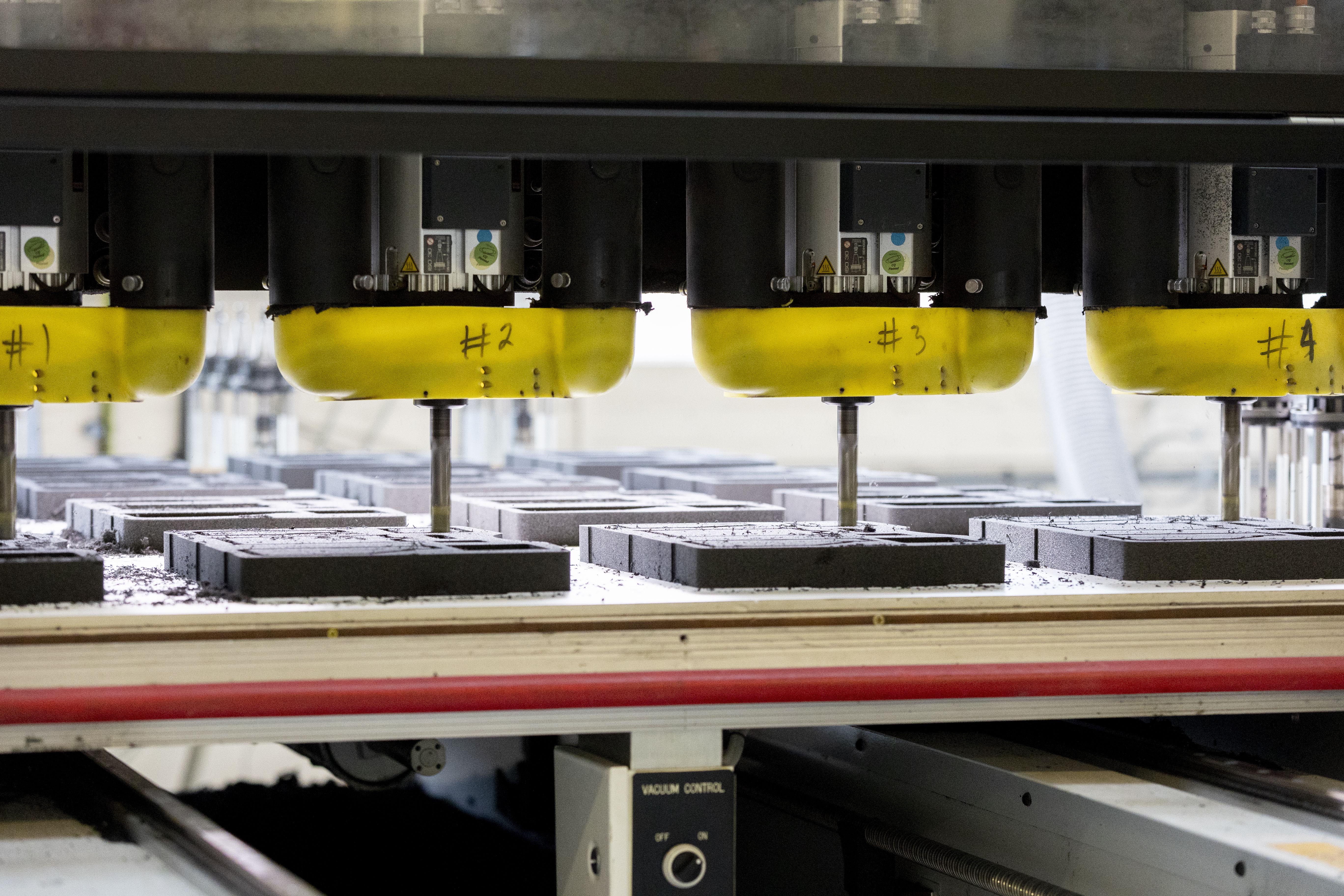
Innovative processes and technologies
Innovation is at the heart of Kewell Converters, with continuous advancements being made to optimise our processes. The implementation of In Process Inspection allows us to monitor and ensure quality throughout every stage of production, minimising errors and maximising efficiency. Additionally, the integration of ‘Maintain X’ software has significantly enhanced our productivity by streamlining workflows, improving accuracy, and reducing waste. These pioneering technologies testify to our commitment to excellence and sustainability.
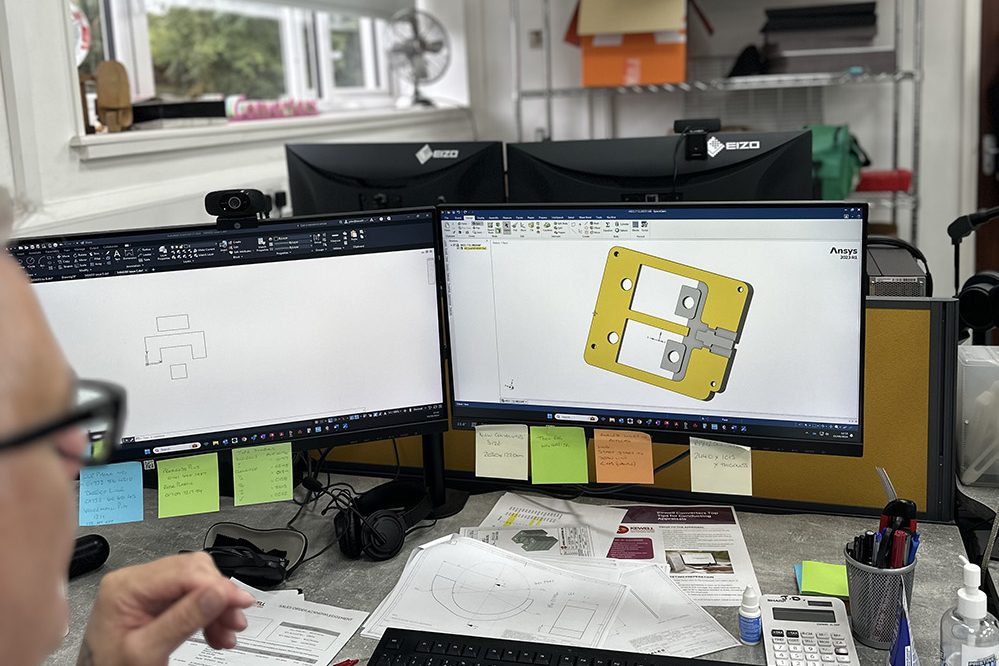
Bringing foam projects to life through CAD design
At Kewell Converters, every foam fabrication project begins as a blank canvas, primed for the bespoke touch of our skilled CAD design team. Our trio of adept CAD CAM (Computer-Aided Design and Computer-Aided Manufacturing) engineers view each project as a chance to craft a solution tailored precisely to your needs.
Whether we’re pioneering concepts from scratch or refining simple sketches provided by our customers, our team excels in transforming ideas into sophisticated designs. Specialising in foam—a dynamic and lightweight material—our engineers bring unmatched expertise to every project. Foam’s propensity to shift requires a nuanced design approach, often necessitating iterative revisions to ensure perfection. This expertise sets our work apart, blending finesse with technical precision.
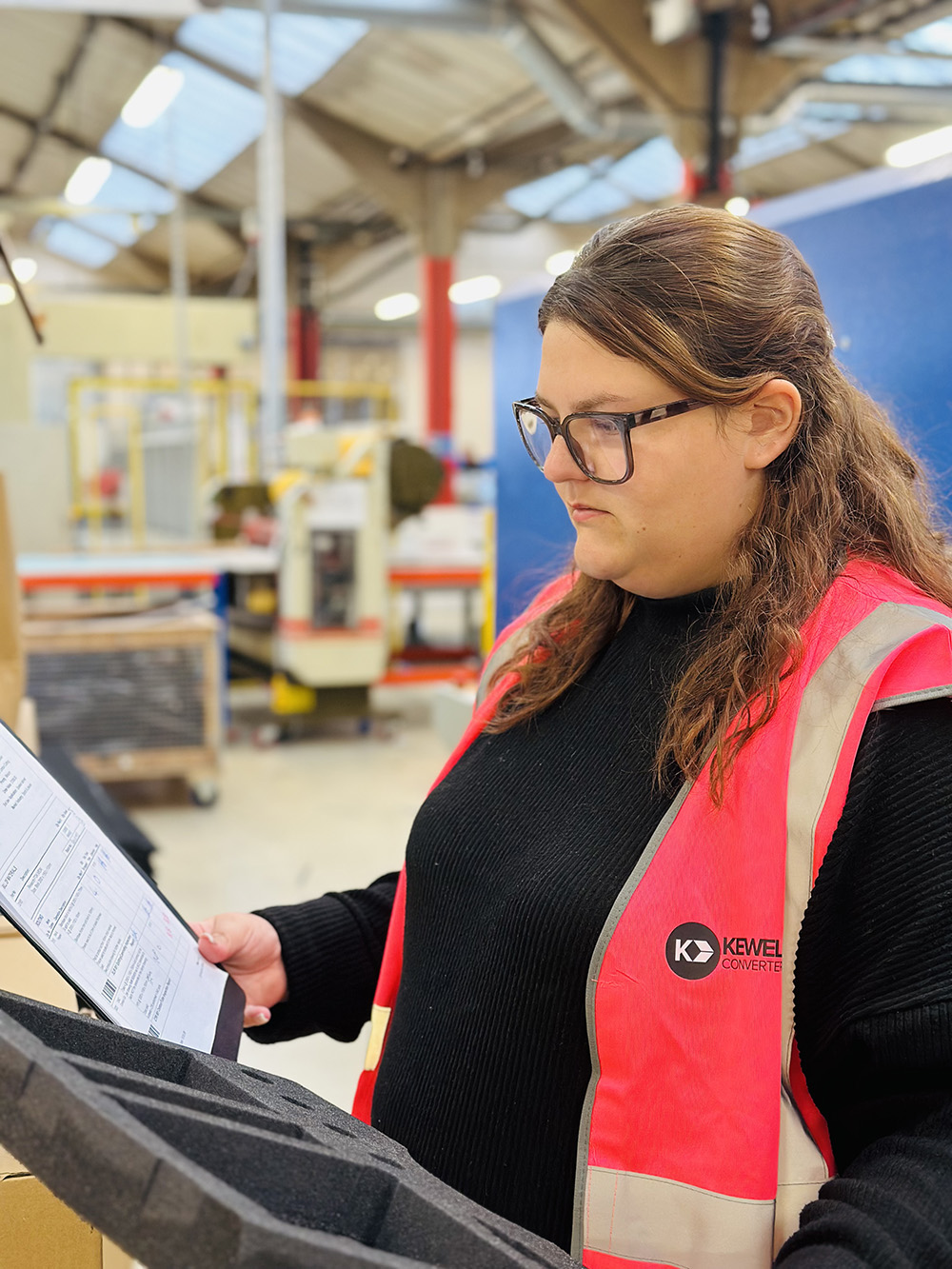
Understanding the importance of customer clarity, we produce both 2D and 3D visualisations using SpaceClaim CAD modelling software. This critical step bridges the gap between concept and reality, allowing our customers to envision the final product with crystal-clear acuity. Our commitment to detail elevates us above the ordinary, embodying the hallmark of engineering excellence. To take concepts to the next level, we create interactive digital designs that enable clients to manipulate and explore the product, gaining a thorough understanding of what will be manufactured.
Continuous improvement and staff development
We believe in the power of continuous improvement and recognise the crucial role of our staff in achieving this and consistently producing products of the highest quality. Comprehensive training programmes are integral to our strategy, equipping staff with the skills necessary to excel in their roles. By setting clear objectives and targets for performance improvement, we maintain a culture of excellence and adaptability.
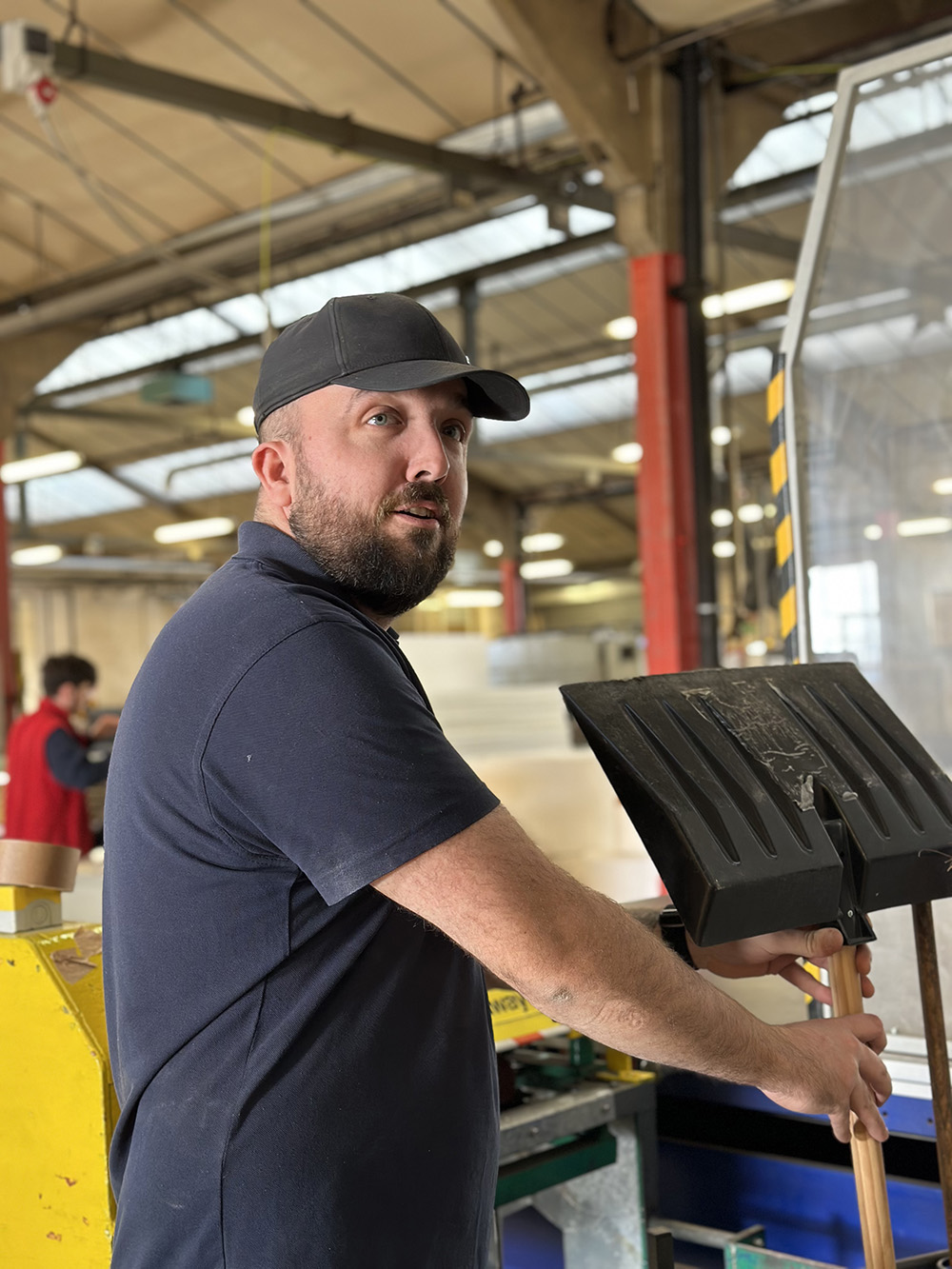
Responding to customer needs
Our customer-centric approach is characterised by a robust process for addressing quality concerns promptly and professionally. We are dedicated to delivering swift resolutions, understanding that responsiveness is key to customer satisfaction.
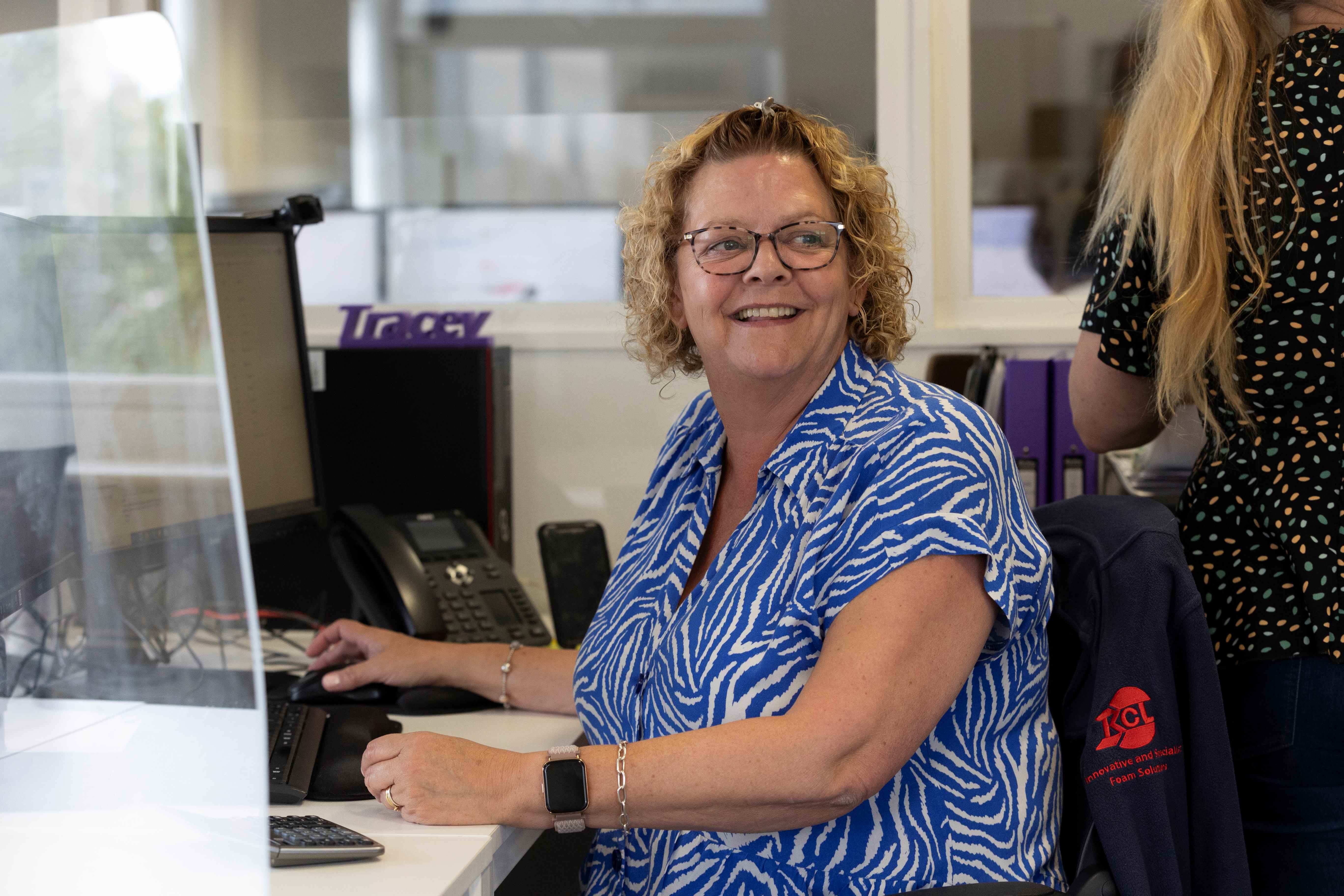
Contact us
For all quality-related queries or to provide feedback, customers can email us here. Our commitment to transparency and open communication ensures that every query is handled with care and professionalism, reinforcing the trust our customers place in us.
Curious to learn more about our design and production process used for foam conversion projects? Get in touch with us today to discuss how we can bring your ideas to life. Email enquiries@kewell-converters.co.uk
Read more how we prioritise health and happiness at Kewell Converters and view our corporate social responsibility.