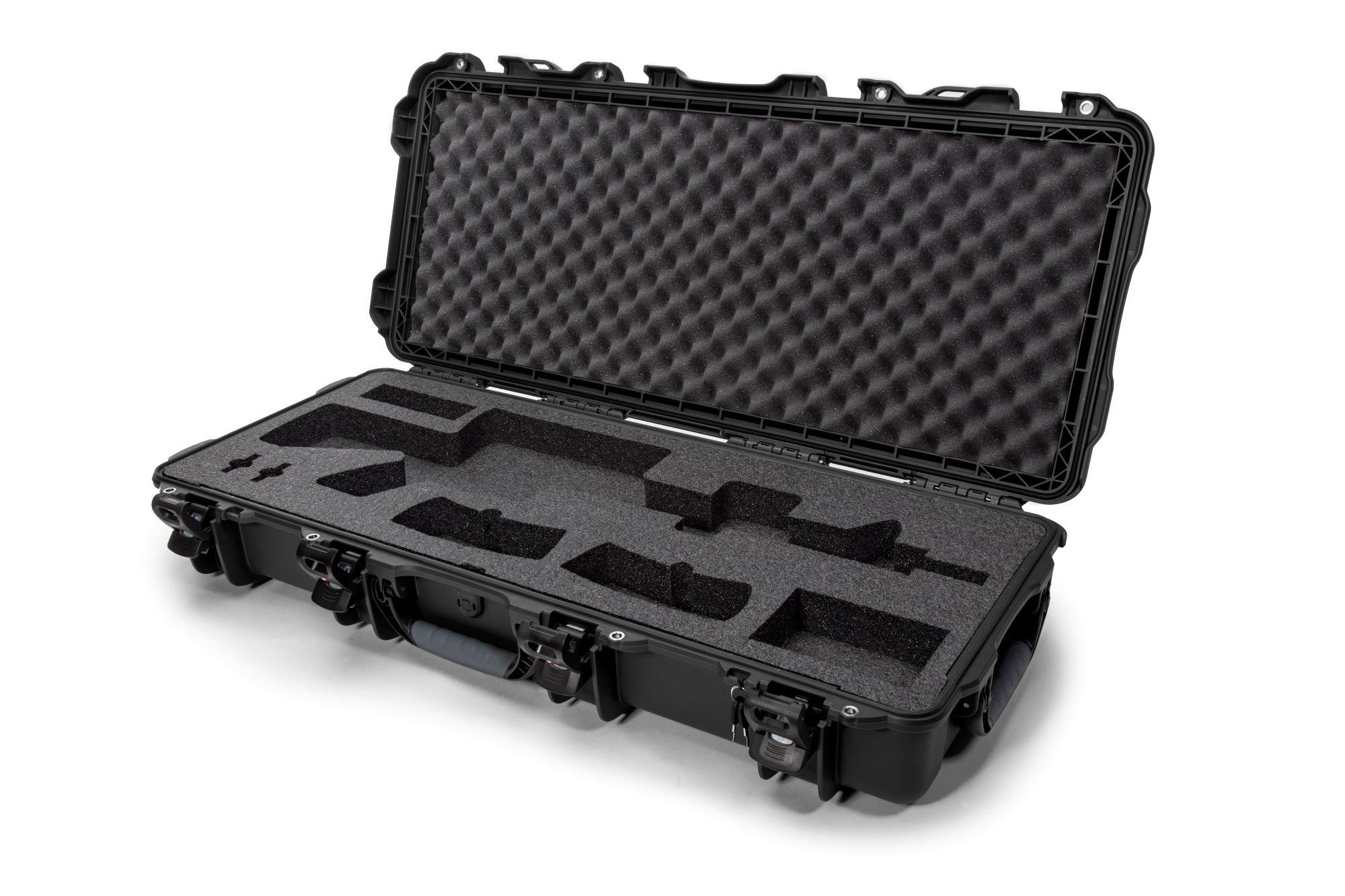
18th March 2025
Kewell Converters and the defence sector: Developing custom military foam solutions
Read more >
Both high density foam and low density foam get a lot of usage globally today. Versatile and easy to adapt, high density foam and low density foam help create options for a broad spectrum of applications, whether that is in an industry like aviation or auto. However, these two types of foam are not the same and each one has different properties that make it suitable for different uses. So, what are the differences?
This is probably the most obvious difference between high density foam and low density foam. A high density foam has almost twice the density of a low density foam. However, it’s worth remembering that density is actually a subjective value and what is high or low will differ for every type of foam. It’s the process of creating the foam that determines where it sits on the high vs low density scale. When the components are mixed together for the foam, the heat causes bubbles to form and this creates thin layers. It’s the proximity of these layers that will make it suitable for high or low density uses.
All foams have different mechanical properties and these differences are especially obvious between high density and low density foams. For example, high density foam has greater mechanical properties. This means that it has more compressive stress resistance, tear strength, tensile strength and thermal shrinkage – among other things – than low density foam.
When it comes to better thermal insulation behaviour it’s low density foam that comes out on top. This is because it has a lower λ-value than high density foam, which means that it has superior insulation properties. So, wherever there is a need for insulation foam, a low density option is likely to be the better choice.
High density foam tends to be harder than low density foam. It’s this softness that makes low density foam the ideal option for something like packaging products or sports mats. High density foam provides a more rigid structure and so is suitable for other applications.
Although any foam can be customised to suit the specific needs of an application, high density foam structure is more rigid, which means that it can be cut into any shape required. High density foam is also suitable for thermoforming, vacuum forming or lamination too.
Due to their different properties high density foam and low density foam have many different applications. While you might find low density foam in packaging and sports mats, high density foam is also widely used, from insulation panels to furniture upholstery. It can be cut, shaped and glued in place (for example where it is being used for insulation).
High density and low density foam are very different in terms of the way that they respond to environments and the properties that they both have. Each one brings different benefits thanks to the major differences between the two, whether that is flexibility or thermal resistance.
Find out more about Kewell Converters High Density Foam and Low Density Foam products or contact our team who can help satisfy your foam needs.
18th March 2025
Read more >
17th March 2025
Read more >
6th March 2025
Read more >