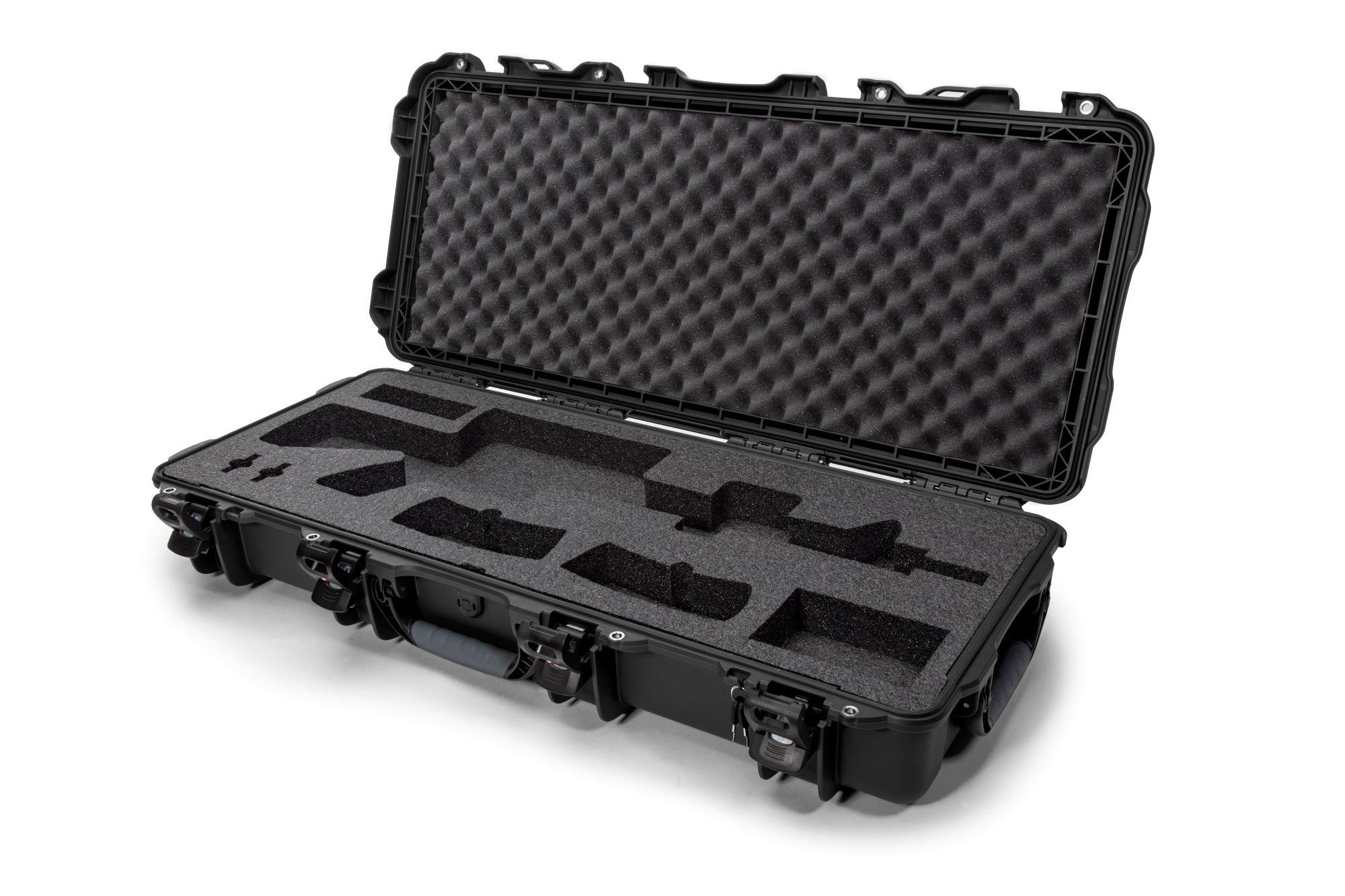
18th March 2025
Kewell Converters and the defence sector: Developing custom military foam solutions
Read more >
At Kewell Converters, the art of manufacturing meets the ingenuity of modern engineering. Today, we’re delighted to introduce you to Omar Gutin, one of our innovative, ambitious manufacturing engineers. Omar’s journey from civil and structural engineering to his current role at Kewell Converters is as inspiring as it is instructive.
Join us as we explore his role, the balance between creativity and technical know-how, and the projects that fuel his passion as well as life outside the work bench.
Q: How long have you worked at Kewell Converters?
Omar: I’ve been with Kewell Converters for one year now.
Q: Where did you work before joining Kewell Converters?
Omar: Before this, I spent two years in civil and structural engineering as a technician at an engineering consultancy firm. It was quite similar in terms of managing projects, but different as I was often on-site taking measurements. I was heavily involved in testing and feasibility studies.
Q: What led you to pursue a career in engineering?
Omar: I studied engineering product design at South Bank University. Initially, I was drawn to civil engineering, but I soon realised it was somewhat limited in scope. I wanted a more design-based role, so I shifted to engineering product design, which offered a broader range of opportunities. Before joining Kewell Converters, I underestimated the versatility of foam. We often think of foam in limited applications like bed foams and cushion foams, but it has a wider scope, including insulation and medical applications.
The role of a manufacturing engineer
Q: How much of your role is creativity versus the technical side?
Omar: I would say it’s about 60-40, leaning more towards creativity. Even when conducting feasibility studies and tests, not everything works as planned, and you need creative solutions to solve problems. There’s a lot of learning through mistakes, which builds your knowledge over time.
Q: Can you describe your role at Kewell Converters?
Omar: I describe my role as similar to that of an inventor. You start with a concept based on an idea and evolve it from the basics. Essentially, I carry complex foam projects from idea to production, focusing on efficiency. There’s a lot of maths involved, with calculations, measurements, and detailed planning.
Q: What does a typical day look like for you?
Omar: I start by arriving at the factory and checking the sales order inbox for pre-production tasks. I assign new jobs to myself, which could be anything requiring a drawing or developing special requirements. I then create a production process and develop solutions to potential problems. On average, I manage about eight new projects a week. I work with fast turnaround times, managing complex, multiple projects simultaneously.
Favourite machines and challenges
Q: Do you have any favourite machines?
Omar: Yes, the Fastweld machine – the world’s fastest polyethylene foam welding machine. The setup and maintenance can be complex, but I’ve become well-acquainted with its workarounds but it’s super efficient.
Q: What are the typical challenges you face on projects?
Omar: Currently, heat embossing is a challenge. The tooling wasn’t as expected, so it’s my job to create a workaround that produces a better quality outcome for the client. Other challenges include creating jigs and fixtures for machines like the Fastweld, which ensure consistency and accuracy in production.
A project to remember
Q: Can you describe a project you’re particularly proud of?
Omar: One standout foam project was developing sound-insulating pads for underwater pumps for Anchor Pumps. This involved working with a new material and creating a screen-printing process to mark the pads efficiently. The project required extensive R&D and resulted in a more efficient production process, producing 2,500 units of high-quality, branded pads.
The future of engineering
Q: How do you see your role and the foam industry changing over the next few years?
Omar: AI has the potential to revolutionise CAD designs, but it requires precise information input. While AI isn’t yet advanced enough to replace all current processes, it’s a promising area. Additionally, there’s a growing emphasis on materials with higher recycled content, which necessitates thorough testing and documentation. For product protection packaging, new materials like mycelium are emerging, although they don’t yet match foam’s durability and shelf life.
Outside work: Powerlifting passion
Q: What do you enjoy doing outside of work?
Omar: I compete in powerlifting, which is a significant commitment as I train four times a week. I have my second major competition coming up, which is a qualifier for nationals. My target lifts are a 240kg squat, a 160kg bench press, and a 270kg deadlift. During competitions, we carefully manage our diet before the weigh-in, then consume high-energy foods like a loaf of bread and honey to fuel our performance.
Omar Gutin’s journey and expertise at Kewell Converters exemplify the innovative spirit and dedication required to excel in manufacturing engineering. His blend of creativity, technical skill, and problem-solving make him a valuable asset to our team. Whether it’s overcoming foam challenges with inventive solutions or pushing the boundaries of material applications, Omar continues to inspire us all.
Stay tuned for more insights and updates from our team at Kewell Converters. For more information about our products and services, feel free to reach out to us directly.
Read more on our blog Showcasing innovation: UK Gasket & Sealing Association members visit and The intricacies of compression moulding
18th March 2025
Read more >
17th March 2025
Read more >
6th March 2025
Read more >