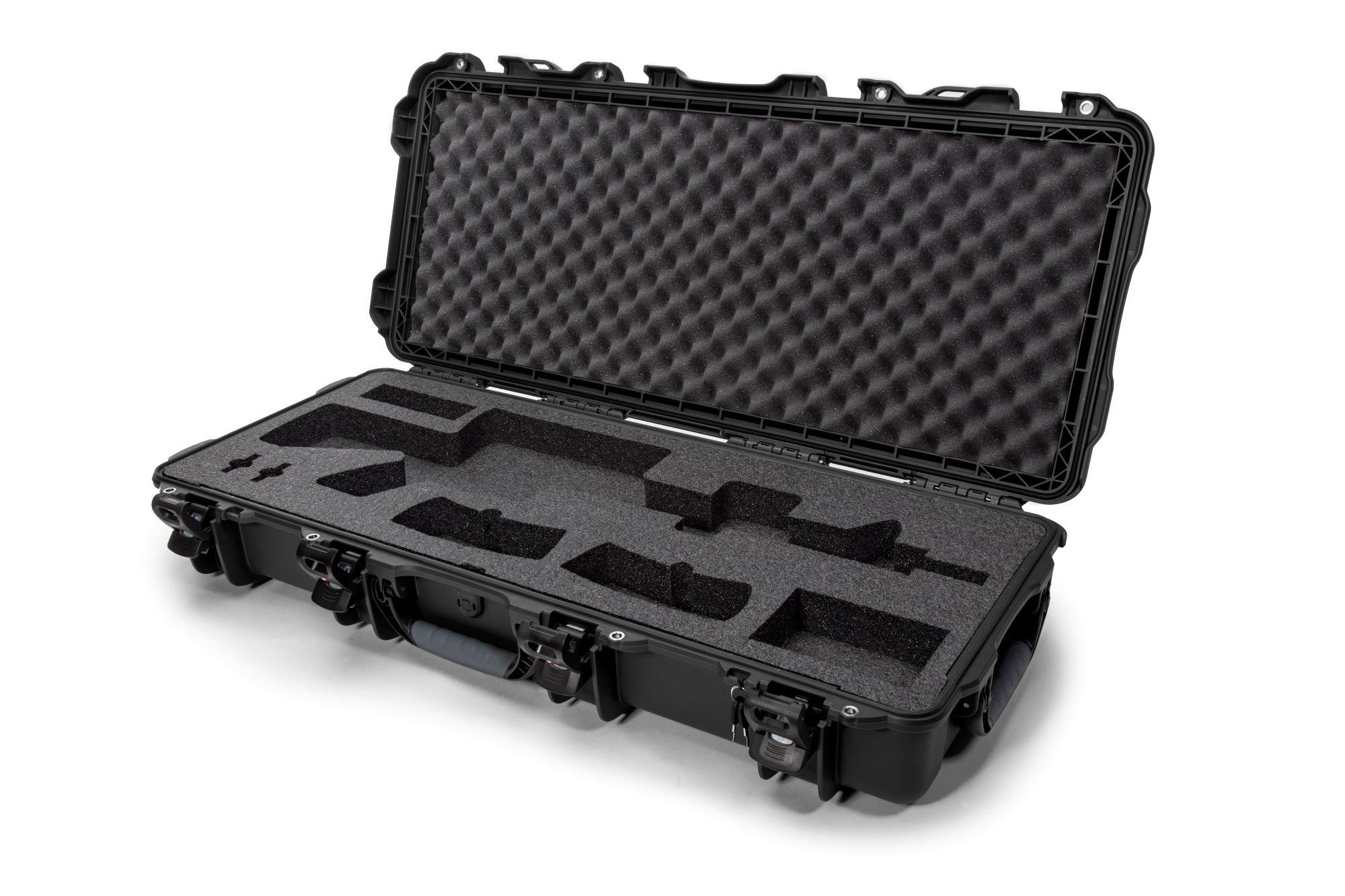
18th March 2025
Kewell Converters and the defence sector: Developing custom military foam solutions
Read more >
From the high-speed circuits of go-kart racing to the meticulous cleanrooms of the pharmaceutical world, the versatility of compression moulding continues to shape the future of manufacturing. Kewell Converters has been at the forefront of this transformation in the UK, meticulously crafting high-performance materials for a variety of applications. We’ll uncover how compression moulding is more than just a process—it’s a craftsmanship that brings designs to life.
Compression moulding is our go to process at Kewell Converters used to forge remarkable three-dimensional foam and composite creations that boast intricate features and exceptional dimensional precision.
The outcome? Exceptionally shaped pieces all without compromising on delicate features or dimensional accuracy. Whether it’s the comfort of helmet padding or the resilience of orthotic supports, compression moulding is the manufacturing muscle behind many of the products that move us, protect us, and improve our quality of life.
While the virtues of compression moulding are vast, they hinge on its cost-effectiveness and the innate strength it imparts to products. This method is a haven for producing larger, uncomplicated shapes that demand flawless structural integrity—and it does so economically.
Neil Johnston, General Manager at Kewell Converters, who has vast experience in thermoplastics says, “we are big fans of the process at Kewell Converters and the results of what can be achieved are quite staggering with perseverance”.
Yet, it would be remiss not to acknowledge the challenges. Complex designs with steep angles or diminutive details are typically beyond its capabilities, and the process isn’t quick. Long cycle times necessitate patience, though this can be counterbalanced with multi-cavity moulds, allowing the creation of numerous parts in a single operation.
Kewell Converters’ mastery of this process shines in our collaborations. Here’s a glance at how we’ve revolutionized the product landscape.
For several years, Kewell Converters has been the driving force behind the seat pads adorning Tillett Racing’s renowned go-kart seats. With champions like Lewis Hamilton and Max Verstappen having experienced their products, nothing less than precision-engineered comfort will do.
But our work goes beyond the race track, extending into long standing collaborations with other premium manufacturers also requiring precision including the design and production of cricket helmets for Masuri, the World’s number one Cricket Helmet Manufacturer, showcasing the adaptability of our processes.
From the specific formulations of racing seat foams to the delicate requirements of the pharmaceutical industry, compression moulding has shown its adaptability and utility. It’s the perfect blend of temperature, pressure, and precision that translates the imagination into tangible, influential products.
The beauty of this craft lies in its commitment to meeting the demands of functionality and design, all wrapped up in the incredible versatility of foam products. Our doors are always open to those who seek to push boundaries and those who need a reliable partner to bring their concepts to fruition. Reach out, and together, we’ll mould a future where quality and precision keep your projects at the pinnacle of performance.
Our team of experts are on hand to offer guidance and insight, ensuring that your next project takes full advantage of this remarkable manufacturing process.
Read about Thermofoams and how we work with the sport and leisure sector.
18th March 2025
Read more >
17th March 2025
Read more >
6th March 2025
Read more >