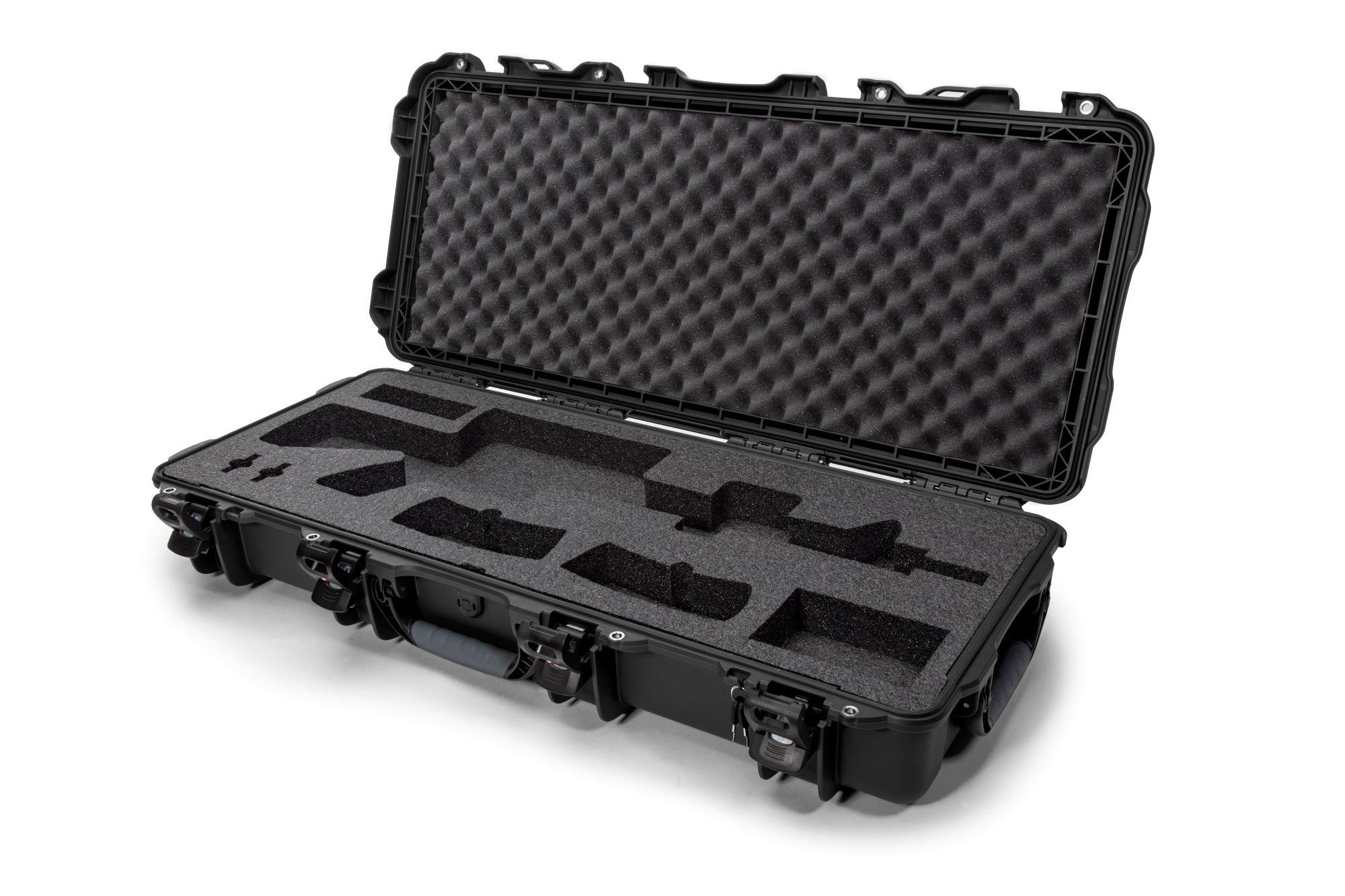
18th March 2025
Kewell Converters and the defence sector: Developing custom military foam solutions
Read more >
In the professional realm, selecting the optimal material for a given application is crucial.
However, many materials falter when exposed to moisture, lack the necessary durability, or simply do not provide the insulation or protection required, leading to inefficiencies and increased costs.
Consider the implications of substandard material choices: compromised structural integrity, safety concerns, frequent replacements, and a potential escalation in long-term expenses. These are not merely financial setbacks but can also impact project timelines and overall quality.
The answer lies in closed cell foam. This material is distinguished by its robustness, superior water-resistance, and exemplary insulating properties.
Whether you’re spearheading an infrastructural project, engineering safety equipment, or seeking a resilient material solution, closed cell foam emerges as the preferred choice.
We invite you to explore this comprehensive guide to understand the multifaceted benefits and applications of closed cell foam, ensuring your projects stand the test of time and efficiency.
Closed cell foam is a type of foam in which the individual cells are sealed off from each other, forming a dense and rigid structure. This unique cellular structure gives the foam its water-resistant, insulating, and durable characteristics. Made from various polymers like polyethylene, polyurethane, and PVC, closed cell foam’s tightly packed cells do not share their internal space with neighbouring cells, making the foam impermeable to water, gases, and other liquids.
This sealed nature of its cells lends the foam certain inherent physical properties, such as increased density and rigidity. Beyond its structural attributes, the foam’s ability to trap air makes it an effective barrier against heat transfer, making it an excellent insulator, especially in construction applications.
Its resilience and moisture resistance grant it a longer lifespan compared to many other foams, leading to its use in a range of applications, from marine and industrial settings to sporting goods and packaging.
The choice of closed cell foam often depends on its intended application, with various formulations tailored to specific needs.
In today’s fast-paced industrial and design landscapes, understanding the materials at our disposal is not just a skill—it’s a necessity. With a multitude of applications ranging from construction to product design, the materials we choose can make or break the success of a project. Within this sphere, closed cell foam has emerged as a frontrunner, offering solutions that are both innovative and efficient.
Unlike many other materials, closed cell foam boasts a long lifespan, reducing the need for frequent replacements.
Its impermeability ensures that it remains unaffected by moisture, making it ideal for environments where water exposure is a concern.
With exceptional thermal properties, it is often the material of choice for insulation projects.
Despite its strength, it’s adaptable and can be moulded into various shapes and forms.
Its weight-to-strength ratio is commendable, allowing for ease in transportation and application.
In the long run, its durability and multifunctionality can lead to significant cost savings.
Many closed cell foams are made from materials that are recyclable or have a reduced environmental impact.
In a world where efficiency, sustainability, and performance are paramount, closed cell foam’s unique properties position it as an unparalleled solution. Our methodical approach to understanding this material will equip you with the knowledge to harness its potential fully.
In the vast realm of materials, making the correct selection for closed cell foam can seem daunting. However, with the right methodology and a unique, comprehensive approach, this task becomes significantly more straightforward.
We’ve curated a specialised selection process, aptly termed the “FoamFit Criterion,” designed to assist you in making choices that are both informed and tailored to your exact requirements.
Begin by understanding the weight-to-volume ratio of the foam. This will give you a clear indication of its strength, resilience, and suitability for projects that demand robustness. Consider the structural demands of your project and ensure the foam aligns with those needs.
Dive deep into the foam’s water resistance capabilities. Especially crucial for applications in humid or moisture-rich environments, this step ensures that the material won’t succumb to water damage or mould, thus extending its lifespan.
Thoroughly analyse the foam’s insulation properties. If your project requires effective temperature control or energy conservation, the foam’s ability to insulate against external temperatures becomes paramount. Look for foams with high R-values for superior insulation.
Assess the material’s adaptability and flexibility. For projects that require custom shapes or intricate designs, it’s essential to choose a foam that can be easily moulded, bent, or shaped without compromising its other properties.
In today’s environmentally-conscious world, it’s crucial to prioritise foams that boast eco-friendly credentials. Whether recyclable, made from sustainable resources, or having a minimal carbon footprint, ensure your choice reflects a commitment to sustainability.
Beyond the initial price tag, consider the long-term value of the foam. Weigh the comprehensive benefits, durability, and potential savings against its upfront cost to ensure that your investment is not only economical but also provides the maximum return over time.
Delve into specific use-case scenarios. Depending on whether you’re using the foam for insulation, cushioning, protective gear, or any other application, ensure that its intrinsic properties align perfectly with the intended purpose.
With this enhanced FoamFit Criterion, you’re not just informed; you’re empowered. This is merely an introduction.
In the intricate tapestry of today’s global industrial landscape, the search for versatile, high-performance, and economically viable materials has intensified. Mastery over materials such as closed cell foam has transitioned from being a mere advantage to an essential expertise. With its plethora of beneficial properties, closed cell foam is seamlessly integrated into myriad industries. This underlines the vital importance of possessing a profound knowledge of its selection, application, and advantages.
Closed cell foam is lauded for its exceptional insulation properties, steadfast resistance to moisture, and commendable structural integrity. In the realm of construction, it provides a robust barrier against external elements, ensuring energy efficiency and structural longevity.
The automotive industry harnesses the power of closed cell foam for padding in seats, offering passengers unparalleled comfort. Additionally, its use in sound insulation ensures quieter rides, while its durability makes it an ideal choice for gaskets and other integral parts.
The marine environment is notorious for its harsh conditions. Here, closed cell foam becomes indispensable for buoyancy aids, given its unique property of not easily absorbing water. This ensures safety and effectiveness even in the most challenging aquatic scenarios.
The medical sector leverages closed cell foam in orthopaedic braces and specific medical devices. The emphasis is on the firm’s ability to offer patient comfort, its adaptability in various applications, and its hygienic properties that prevent microbial growth.
Athletes and enthusiasts alike benefit from the shock-absorption and protective qualities of closed cell foam. From protective gear to mats and other equipment, its versatility ensures safety and enhances performance.
The delicate dance of logistics and product transportation relies heavily on closed cell foam to safeguard fragile items. Its superior cushioning properties combined with its lightweight nature make it the go-to choice for ensuring products reach their destination unscathed.
The aerospace industry, with its rigorous standards, opts for closed cell foam for insulation and protective padding within aircraft. This choice stems from the material’s impressive strength-to-weight ratio and its ability to provide consistent thermal insulation at high altitudes.
In the face of such expansive applications across varied industries, a systematic, in-depth approach to understanding closed cell foam is paramount. Our method, refined through rigorous research and real-world applications, offers an unparalleled deep dive into this material. By immersing yourself in our comprehensive guide, you equip yourself with the acumen to implement closed cell foam solutions adeptly, ensuring industry-leading results and innovation.
As we conclude this insightful journey into the world of closed cell foam, it’s evident that its multifaceted applications and inherent benefits make it a cornerstone material for diverse industries. Mastery over such a versatile material not only equips businesses with the tools to innovate but also positions them at the forefront of efficiency and sustainability.
Our deep-rooted experience and expertise in this domain aren’t just theoretical; they stem from years of hands-on engagement, rigorous research, and countless successful applications. This positions us uniquely to guide, advise, and offer solutions that are both practical and transformative.
Kewell Converters stands as a beacon in this arena. With a legacy of excellence and a commitment to quality, Kewell Converters is not just a supplier but a partner in your journey. They understand the intricacies of closed cell foam and are dedicated to assisting you in finding the perfect fit tailored to your business’s unique needs.
By entrusting your requirements to Kewell Converters, you’re ensuring that your projects are backed by unparalleled expertise and a commitment to excellence. Navigate the future with confidence; let Kewell Converters be your compass in the world of closed cell foam.
Closed cell foam is renowned for its versatility. It’s particularly valued for its excellent insulation properties, water resistance, and durability.
While closed cell spray foam offers numerous benefits, there are scenarios where its use might not be ideal. Firstly, it’s generally more expensive than open-cell foam. Secondly, due to its rigidity, it might not be the best choice for areas requiring flexibility. Also, improper installation can lead to off-gassing, which can affect indoor air quality.
Closed cell foam is water-resistant, meaning it doesn’t easily absorb water. While it can act as a barrier against moisture penetration, it’s not a direct solution for fixing active leaks.
Foam insulation, while beneficial in many respects, does have some drawbacks. It can be more costly than traditional insulation methods. Improper installation can result in gaps or off-gassing.
Closed-cell foam is known for its longevity. Depending on the application and environmental factors, closed-cell foam can last for decades.
While there are DIY spray foam insulation kits available in the market, it’s generally recommended to have it installed by professionals. This ensures even application, adherence to safety guidelines, and reduces the risk of improper installation which can lead to gaps or potential off-gassing.
Considering the complexities and technicalities associated with closed cell foam, always consult with experts like Kewell Converters for tailored advice and solutions.
18th March 2025
Read more >
17th March 2025
Read more >
6th March 2025
Read more >