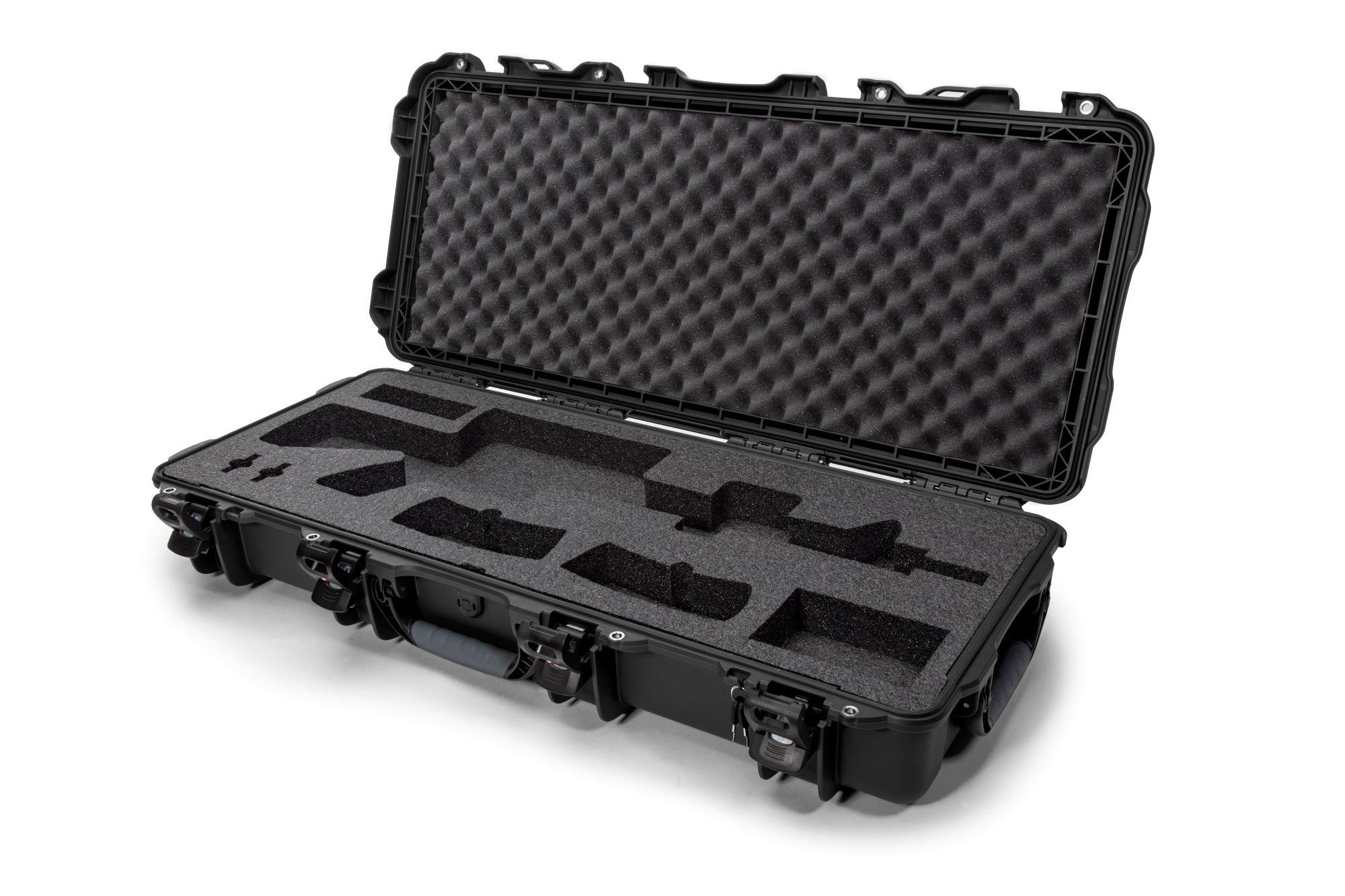
18th March 2025
Kewell Converters and the defence sector: Developing custom military foam solutions
Read more >
The process of foam conversion is what enables custom foam solutions to be designed for just about every need. Foam converters play a key role in ensuring that foam is ultra versatile – and that it can be used for anything, from packaging to cars, PPE and bedding. When it comes to creating foam solutions, foam converters have a key role to play.
It is essentially any process that can be used on foam blocks to create pieces of particular sizes, dimensions and features. This could be something as simple as splitting, for example, which is where large foam blocks are split down into sheets of foam. Where a sharp blade is used to cut foam down to size this is called band-knifing and is also part of the foam conversion process. Other cutting processes that are involved in foam conversion include die cutting, log cutting, routing and contour cutting. Other phases of foam conversion can include:
Foam converters are vital for making any foam fit for purpose and that includes some of the most commonly used foams, whether that is neoprene (formulated for its resistance to oils and chemicals), PVC foam – which is incredibly widely used because of its softness and flexibility – as well as silicone, which is a closed cell foam with especially stable and non-reactive properties. Other types of foam that frequently go through the foam conversion process include ethylene propylene diene monomer (EPDM), vinyl and polyurethane foam. The foam conversion process may involve using more than one type of foam at a time in order to create custom solutions.
Foam converters make it possible for custom foam solutions that appear across many industries and sectors. These include:
Foam converters make custom foam solutions possible, transforming blocks of many different types of foam into products and components that are used across many different sectors.
Find out more about how Kewell Converters can help you with your specialist foam conversion need Contact us today.
18th March 2025
Read more >
17th March 2025
Read more >
6th March 2025
Read more >